PC210LCi-11: All the features and benefits of a PC210LC-11…plus intelligent Machine Control
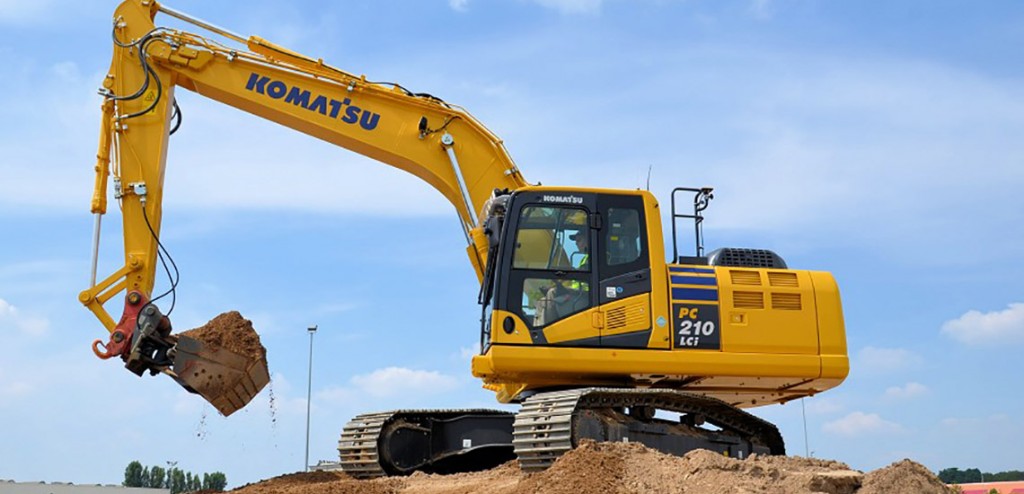
The Komatsu PC210LCi-11 integrates all the benefits of the standard PC210LC‐11 excavator but with the extra advantage of Komatsu’s unique intelligent Machine Control technology, a now proven concept that has penetrated markets worldwide. The exclusive control function allows the operator to no longer worry about digging too deep or damaging a target surface. From rough digging to finish grading, the PC210LCi-11 excavator can dramatically improve efficiency, precision and safety on a work site.
Mal McCoy, Product Manager at Komatsu Europe says:
“The LCi‐10 excavator has already proved to be a ‘game changer’ in how job sites are managed, with efficiency and productivity increased and resource costs lowered. The new PC210LCi‐11 now raises the bar even higher, thanks to improved performance and the addition of the Auto Tilt Bucket. It’s the only hydraulic excavator currently on the market capable of semi‐auto operation”.
The PC210LCi-11 is available with the Komatsu tilt bucket. Necessary for PC210LCi-11 operators, (over 70% avg. usage in EU.), the Komatsu tilt bucket allows to change the bucket angle in real time to match the design surface during Semi‐Auto function. The bucket uses integrated stroke sensing tilt cylinders to determine accurate positioning. The flexibility of the PC210LCi‐11is greatly increased, allowing complex surface designs without the need to change the position of the machine constantly.
Operating weights of the PC210LCi-11 range from 22.120 ‐ 23.580 kg, depending on the configuration. The fuel efficient EU Stage IV Komatsu SAA6D107E‐3 engine puts out a net 123 kW / 165 HP @ 2.000
rpm. Other specifications are identical to those for the Komatsu PC210LC‐11.
The latest KOMTRAX™ telematics, and the Komatsu Care® complimentary maintenance program, offer top fleet management and support, protect the machine against misuse and guarantee maximum efficiency and uptime.
Innovative: Automatic Real Time Digging Control
With the world’s first intelligent Machine Control excavator, the bucket is automatically limited from digging beyond the target surface. The control function maintains grade automatically, with real‐time bucket edge positioning in relation to the machine and the job surface. Status is instantly displayed on the full colour, multi‐function 12.1” control box monitor, eliminating the wait time associated with conventional sensors.
Integrated: Standard Factory Installed Integrated Machine Control System
Factory installed, Komatsu’s fully integrated intelligent Machine Control system includes stroke sensing hydraulic cylinders for the boom, arm and bucket, newly developed by Komatsu for precise real time bucket edge positioning. The IMU (Inertial Measuring Unit) gives precise machine orientation and determines machine angle from gyro and accelerometer data. High performance antennae send satellite signals to a GNSS receiver that processes them and provides real time position of the machine.
Intelligent: Enhancements for Optimized Performance
The Komatsu PC210LCi‐11 intelligent Machine Control excavator lets the operator focus on moving material efficiently, with no worry about digging too deep. The touch screen control box monitor, makes grading easy and accurate with a facing angle compass, a light bar and audio guidance. Information such as real‐time “as‐built” status, a magnified fine grading view or a 3D bird view can be displayed simultaneously.
By setting 3D design data on the control box monitor, staking can be reduced or eliminated, as can surveying and final inspection. Safety is greatly improved, with less people needed on the job site and near the machine.
Intelligent ON/OFF switches for the semi‐automatic function, but also to raise/lower the design offset, are now fully integrated in the joysticks. This further increases efficiency and safety for the operator.
Benefits
The unique benefits of Komatsu’s intelligent Machine Control system on the new Komatsu PC210LCi‐11excavator are summarized by an outstanding improvement in productivity. This is achieved by consistent accuracy when rough digging, and by completing final grade automatically in just one pass. Cycle times and operator performance are thus improved with a reduced risk of error, and lower costs for fuel, labour and increased machine utilisation.