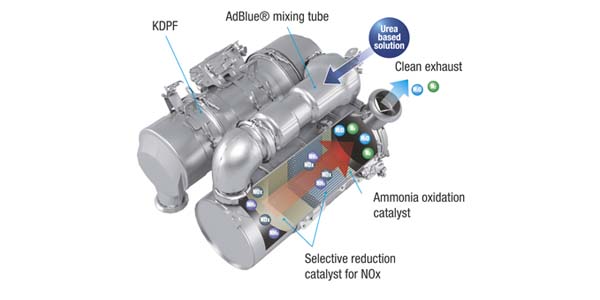
Not so long ago, earth moving machines (as well as busses and trucks) used to belch out plumes of black smoke from their exhausts. Consequently, damaging the air quality and emitting high quantities of non-visible Nitrogen Oxide (NOx), contributing towards the negative impacts of global warming.
Now this particular matter (soot) is trapped within the Diesel Particulate Filter (DPF).
The DPF is a device which is fitted into the exhaust system and contains a ceramic honeycomb type filter. The porous nature of the ceramic allows the exhaust gasses to pass through the filter. But any soot is too large to pass through the porous ceramic so is captured within the DPF.
Our DPF is also designed to run at a very high temperature so that captured soot degrades within the device leaving only a residue of ash. Ash cannot be removed, so we have planned a procedure to replace the DPF during 4,500 hour service and a second at 9,000 hours free of charge with the complementary Komatsu Care maintenance plan that comes with all new wheel loaders.
Our DPF is sent back to the Komatsu facility within the KGC factory at Hannover where it is refurbished and can be put back into our parts system for the next 4,500 hour service.
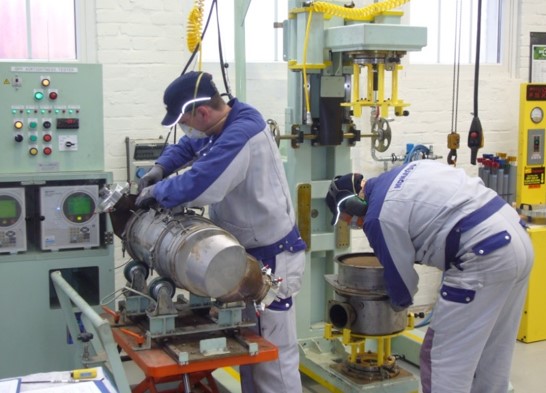
So far the exhaust gasses from the engine have been cleaned in the DPF. They now pass through the exhaust system free of soot and enter another device called a Selective Catalytic Reduction (SCR).
The stringent legislation on exhaust gas emission within the EU not only challenges manufacturers to ensure the exhaust gasses are clean but also challenges the chemical make-up of the gas –Nitrogen (NOx) Oxide damages the Ozone layer and leads to Global warming, so the legislation limits the amount of NOx that the machine is allowed to emit.
This is even more clever than the DPF as within our exhaust system there is a catalytic converter, the machine sensors monitor the gas flow and automatically inject a controlled amount of Diesel Exhaust Fluid DEF (or AdBlue as it is commonly known) depending upon the exhaust gas flow rate.
The DEF chemically reacts with NOx laden exhaust gas, and together with the heat the catalytic converter generates, converts the ozone damaging NOx into water (H2O) and non-toxic nitrogen gas (N2).
The challenge all machinery suppliers face with DEF is that it is prone to crystallisation, so when our machine’s ignition is switched off the system purges the feed pipes and hoses and empties the DEF back to tank. As part of the complimentary Komatsu Care cover we will conduct a DEF tank flush at 4,500 hours and again at 9,000 hours where we also flush the feed pipes and hoses.