Please note that this article is not about the latest model of this machine. Please view our current range of wheel loaders here.
The highly versatile Komatsu WA320-7 wheel loader features a perfect mix of power, comfort and reliability. Replacing the popular WA320-6, it has an EU Stage IIIB emission certified engine, with ‘Komatsu SmartLoader Logic’ engine control. Plus an advanced hydrostatic drive line to offer exceptional tractive force and ultra-low fuel consumption. The WA320-7 sets new efficiency standards for wheel loaders.
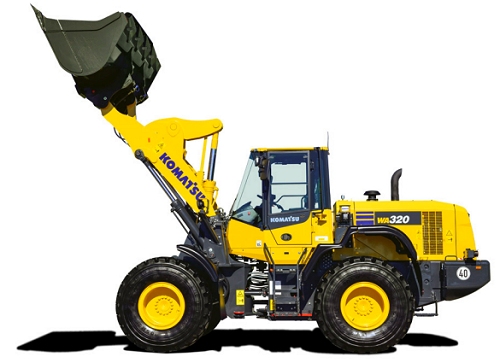
With a net horsepower of 127 kW (170 hp), the WA320-7 is powered by a Komatsu SAA6D107E-2 engine. Komatsu has leveraged its leadership in technology and innovation to design a more environmentally friendly engine which decreases fuel consumption by up to 10 percent and increases the engine torque up to 12% compared to the WA320-6.
With an operating weight of 15 – 16 tonnes, the new wheel loader features improved efficiency, lower fuel consumption, improved operator comfort, and enhanced serviceability to maximize productivity while lowering operating costs.
The WA320-7 is supported by Komatsu CARE, a complimentary maintenance program for Komatsu customers that comes as standard with every new Komatsu EU Stage IIIB construction machine. For the first three years or 2.000 hours it covers factory-scheduled maintenance, performed by Komatsu-trained technicians with Komatsu Genuine parts. Komatsu CARE offers up to a maximum of two complimentary Komatsu Diesel Particulate Filter (KDPF) exchanges and a KDPF warranty for the first 5 years or 9.000 hours.
Equipped with the latest Komtrax™ technology, the WA320-7 sends machine operating information to a secure website utilizing wireless technology. Data such as operating hours, fuel consumption, location, cautions and maintenance alerts are relayed to the web application for analysis. The KOMTRAX™ fleet monitoring system increases machine availability, reduces the risk of machine theft, allows for remote diagnosis by the distributor, and provides a wealth of other information to drive business efficiency and productivity.
One machine for all applications
The WA320-7 utilizes the versatile Parallel Z-bar (PZ) loader linkage. It provides the added advantage of parallel lift for pallet moving and high tilt forces to handle large attachments. The PZ linkage also offers large break-out forces to make bucket filling easy and quick. Ideal for loading material and earthmoving jobs, its lift force at top is increased by up to 10% compared to the WA320PZ-6 for improved digging performance.
New features of the WA320-7 include:
SmartLoader Logic
The WA320-7 features Komatsu SmartLoader Logic, which provides optimal engine torque for the job required. Komatsu SmartLoader Logic helps save fuel by automatically decreasing engine torque when the loader isn’t working hard, such as when it is driving with an empty bucket. Komatsu SmartLoader Logic functions automatically and doesn’t interfere with operation, saving fuel without decreasing production.
Responsive Hydrostatic Powertrain System
Now in its 3rd generation, the Komatsu hydrostatic (HST) drive train features increased pump capacity for higher efficiency and responsiveness. The self-braking effect of the HST drivetrain slows down the machine when the accelerator is released. Additionally, brake wear is practically eliminated. Control is enhanced which is especially important when working in tight places.
The electronically controlled HST drivetrain features the Komatsu Traction Control System (K-TCS) and facilitates operation in soft or slippery ground. Simplified traction controls feature 3 settings: MAX, AUTO and S-Mode. The Variable Speed Control (VSC) allows the operator to set a speed up to 8.1 mph for applications such as mowing or broom use. For slower speeds, the creeping speed range sets a speed up to 1 km/h.
Convenient Maintenance and Serviceability
The WA320-7 provides easy service access to reduce downtime. The new wheel loader has a wide cooling fin spacing and a standard auto-reversing fan to help keep the radiator clean. The machine is equipped with the exclusive Komatsu EMMS (Equipment Management Monitoring System), which provides enhanced diagnostic features that give the operator and technicians greater monitoring and troubleshooting capabilities. EMMS also continuously monitors all critical systems, as well as the planned maintenance schedule, and provides troubleshooting assistance to minimize diagnosis and repair time.
Enhanced Operator Environment
The new cab provides a more comfortable and quieter work environment so the operator can maximize productivity. For improved visibility, the front glass has been lowered and the dashboard has been redesigned. A new redesigned right hand console has a multi-function mono-lever with proportional control for the integrated 3rd spool. An auxiliary input has also been added to connect an MP3 player or other device along with two 12-volt ports that have been incorporated into the cab.
The high-resolution 7” LCD monitor features enhanced capabilities and displays information in 25 languages for global support. Using the monitor, the operator can easily modify settings for items such as the new Auto Idle Shutdown or the auto-reversing fan. Operators can also check operational records, such as working hours or fuel consumption; monitor the KDPF soot load; or check how much time is required before the next maintenance interval. Additionally, the monitor offers the operator the option of using the ECO Guidance function, which will provide operational tips to reduce fuel consumption. A high-resolution back-up camera is standard with every machine and the separate monitor is mounted on the right hand side of the console for operator convenience.
EU Stage 3B Emission Certified Engine
Built upon proven Tier 3 technology, the SAA6D107E-2 engine provides lower emissions while also lowering fuel consumption. The Komatsu EU Stage 3B engine uses an advanced electronic control system to manage air flow rate, fuel injection, combustion and exhaust after treatment to optimize performance, reduce emissions, reduce fuel consumption and provide advanced diagnostic capability.
As a leader in hydraulic technology, Komatsu has developed a hydraulically actuated Komatsu Variable Geometry Turbocharger (KVGT) and an Exhaust Gas Recirculation (EGR) valve, resulting in better precision and air management as well as longer component life. The Komatsu Diesel Particulate Filter (KDPF) has an integrated design that will not interfere with daily operation but will keep the operator aware of its status. This smart system enables a high percentage of passive regeneration.