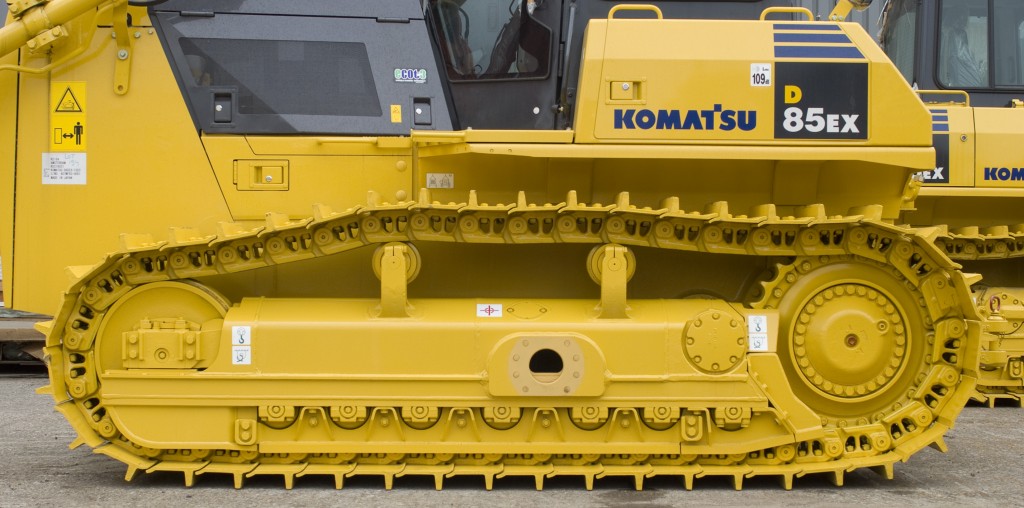
Undercarriage Maintenance
Here at Marubeni-Komatsu, we understand that the undercarriage can represent 50% of a machine’s maintenance expenses.
By following these undercarriage maintenance tips, you can get a better performance and life out of your undercarriage and help to reduce those overall maintenance costs.
Routinely inspect the undercarriage
It is important during undercarriage maintenance to complete a full undercarriage inspection for excessive or uneven wear, as well as look for damaged or missing components.
The following items should be inspected on a routine basis:
• Drive motor
• Drive sprockets
• Main idlers and rollers
• Rock guards
• Track bolts
• Track chains
• Track shoes
• Track tension
Ignoring damage and wear on smaller components could indicate or lead to more complicated, costlier problems.
Keep the undercarriage clean
If you allow the tracks to build up with dirt, mud, and other debris it will lead to premature wear on its components. Debris on the undercarriage can also make the machine feel less powerful and can also increase fuel usage. At the beginning or end of each day operators should spend some time cleaning the undercarriage – shovels and pressure washes can be used to assist with the cleaning.
Track adjustment
Incorrect track tension may lead to increased track wear, so it is important that you keep your tracks to the correct adjustment at all times. Refer to your Komatsu Operation & Maintenance Manual for your machine for details of the correct adjustment and how to achieve this.
The correct shoe width
Choose the proper shoe width by considering the weight of the machine and application. For instance, narrower excavator shoes are better suited for hard soil and rocky conditions because they have better soil penetration and grip. Wide excavator shoes typically work well in soft underfoot conditions because they have more flotation with lower ground pressure.
Consider rubber tracks for sensitive surfaces: These are available on smaller excavators and excel in a variety of applications. Most noticeably, rubber tracks provide good flotation, allowing excavators to travel across and work on soft ground conditions. The rubber tracks have minimal ground disturbance on finished surfaces, such as concrete, grass or asphalt.
Best basic practises for operators
Reduce speeds – As machines accelerate they wear the bushings, sprockets and pins.
Minimise reversing – The tracks on your machine are designed to operate with less wear when travelling forward compared to reverse travel, so you should only reverse when required.
Make wider turns – Sharp turns or pivoting the machine can lead to accelerated wear and increase the potential for de-tracking.
Minimise time on slopes – Operation time on sloped ground conditions, which increases wear on rollers, idlers and guide lugs.
Avoid obstructions – as well as uneven ground.
Planned maintenance
You should ensure that you get your undercarriage components checked regularly by a specialist.