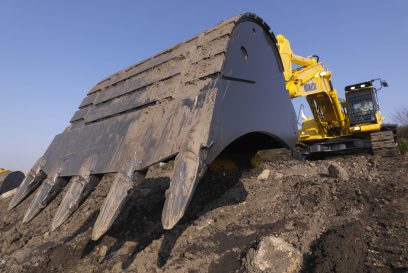
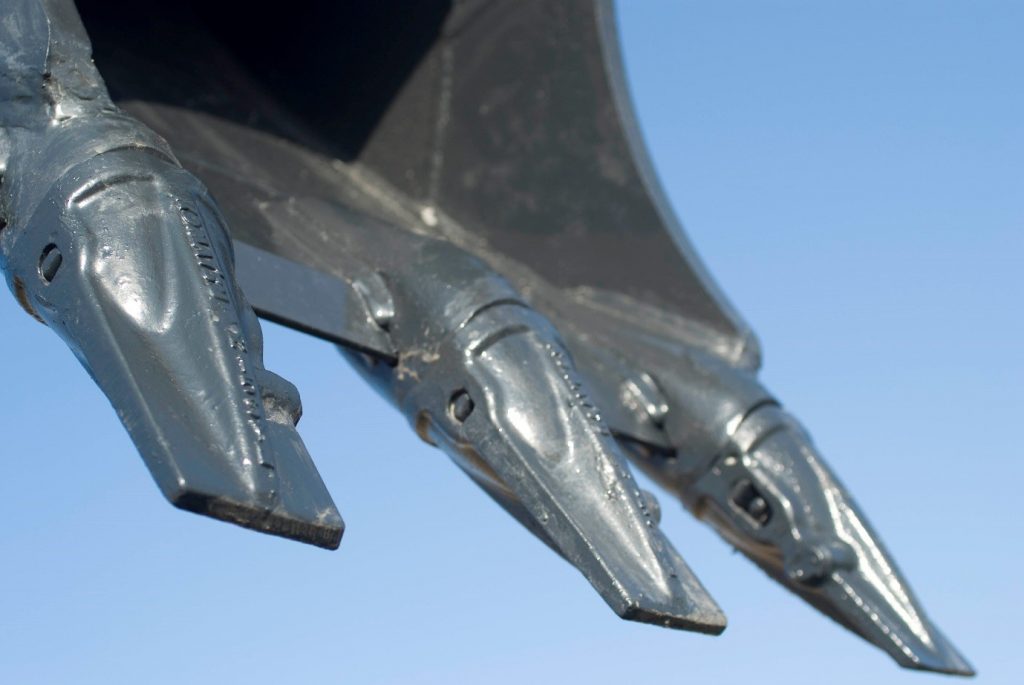
Marubeni-Komatsu Ltd recognises that all companies need to stay competitive by reducing costs. Here are a few tips for how you may be able to save money on operating costs by reducing machine downtime and shortening production cycles.
1. REGULAR INSPECTIONS
Major cracking, loose components and faults can all be prevented by regularly inspecting your ground engaging tools. Since the operator knows the machine better than anyone else, encourage them to complete 5-minute visual inspections at the start and end of their shift will help identify any damage or excessive wear early on and before it becomes a costly fix.
Alternatively, you can contact us to arrange a bucket inspection from a Komatsu specialist.
2. EXTRA PROTECTION
Make sure your bucket reaches its expected wear life – even in tough applications – by purchasing extra protection such as shrouds or choccy bars. This short term cost will reduce damage and extend the life of your attachment.
3. INVEST IN QUALITY
At Marubeni-Komatsu we only sell high quality products from either Komatsu or trusted suppliers. Whilst there is usually very little difference when comparing two parts visually, opting for a low cost alternative usually impacts the quality which increases the risk of accidents and leads to high maintenance costs for almost all applications.
Always calculate the long-term costs rather than the bottom-line price.
4. PREVENTION IS KEY
Daily inspections are great but by also implementing a ground engaging tools maintenance strategy you can improve unplanned equipment downtime further. With a preventative strategy in place, regular interventions are undertaken to avoid unexpected breakdowns and the costs that go with them.
Need some advice? Marubeni-Komatsu offers an inspection programme for fleet users which assists you to plan for future budget costings. Speak to your local PSSR for more information.
5. 1 PIN FOR EVERY 4 TEETH
Don’t assume that pins are needed every time new teeth are purchased. Reusable pins provide substantial savings due to outlasting the teeth several times over. For example, the pins that come with the Kmax tooth system can be reused 4 times on average depending on the application.
The G.E.T. prevention strategy (as discussed in point 4) can include the regular counting of how many times a pin has been used in order to predict when they should be replaced.
Want to introduce Kmax? – click here for a free quote on a First Fit Kit!
6. HAMMER TIME IS HISTORY
A hammerless system provides a safe and quick installation & replacement advantage over other systems. Costs are reduced by removing the need of special tools and health & safety gear – only basic glasses and gloves are required.
7. DON’T COUNT THE COST
Anyone can obtain production data but the real value is using the data to support decision-making. When reviewing ground engaging tools performance & usage, it is recommended to look closely at the cost-per-ton/cost-per-hour which can determine the correct G.E.T. to use
Incorrect G.E.T. choices can result in more fuel use, reduce engine and power train life and also increase operator fatigue.
8. SWITCH POSITION OF TEETH
Teeth can wear irregularly depending on the application with some wearing much faster than the others. Swap the position of the highly worn teeth with the lesser worn teeth on the bucket to improve the edge of the bucket and fill rate whilst also reducing teeth breakages. Most often it’s the outer teeth that tend to wear quicker than the inner ones so swapping them around can reduce the number of teeth purchased throughout the year.
9. CHOOSE A REVERSIBLE TOOTH SYSTEM
Another option for solving irregular tooth wear can be choosing a tooth system whereupon the teeth can be reversed.
Kmax Rock Chisel (RC) are symmetrical – check out this article
10. ONGOING TRAINING AND MONITORING
Finally you can always benefit from training the operator in tooth change-outs & machine inspections can reduce significant downtime by spotting small issues before they turn into serious malfunctions.